The latter has been a mainstay of the Airshow since its birth in 2008. Every year, the Straits Times snaps about 700,000 pictures of the RSAF doing cartwheels in the sky and farting rainbows from their tail-end. The remaining 300,000 photos are devoted to grounded fighter jets and dudes in khaki flight suits.
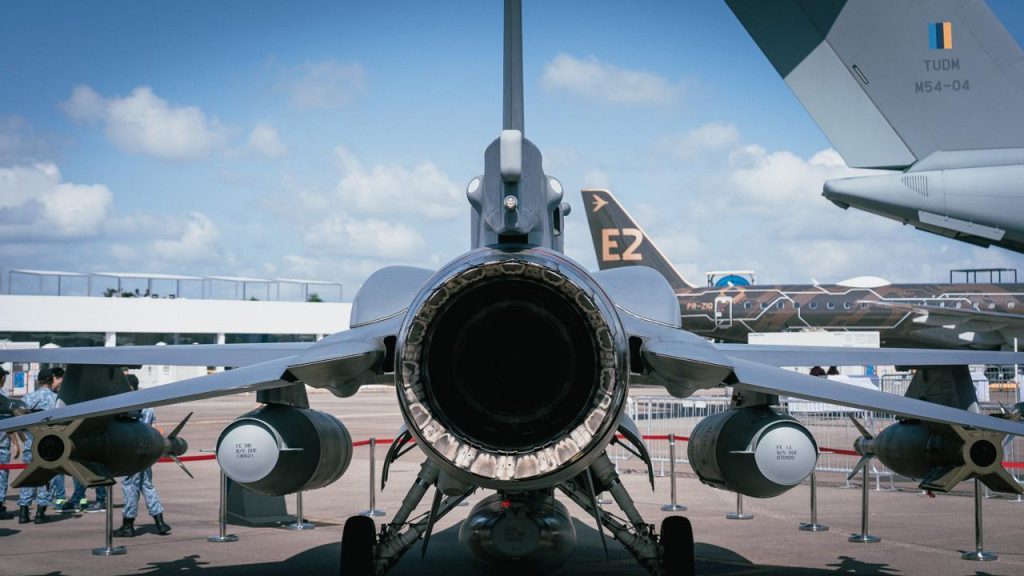
In reality, however, aerial pole-dancing was never the event’s main focus. For one week prior to the flying displays, it is a trade show of the most orthodox variety, held at a location so ulu you cannot get a Grab in or out. The journey by taxi takes the better part of an hour. The registration, security, and temperature screening, another twenty minutes or so.
The entire process is eerily reminiscent of flight boarding. Whether this is coincidence or by design, I do not know. But it’s uncanny. There is a check-in aisle and many, many Certis Cisco officers. Executives in blazers roam the cavernous exhibition space in packs, talking in low voices about MRO or CAA. They could be business travellers in any transit lounge in the world.
In place of duty-free shopping outlets, there are booths—huge booths that dwarf your average airport Rolex boutique. You might not understand what they’re selling, but the scale is undeniably impressive. Rolls-Royce’s pavilion has a two-storey tall jet engine. Boeing has built an entire condo show-flat complete with Barcelona chairs and wall-mounted LED TVs. If not for the fact that multibillion-dollar deals are sealed at the Airshow every year, I would call the architecture megalomaniacal.
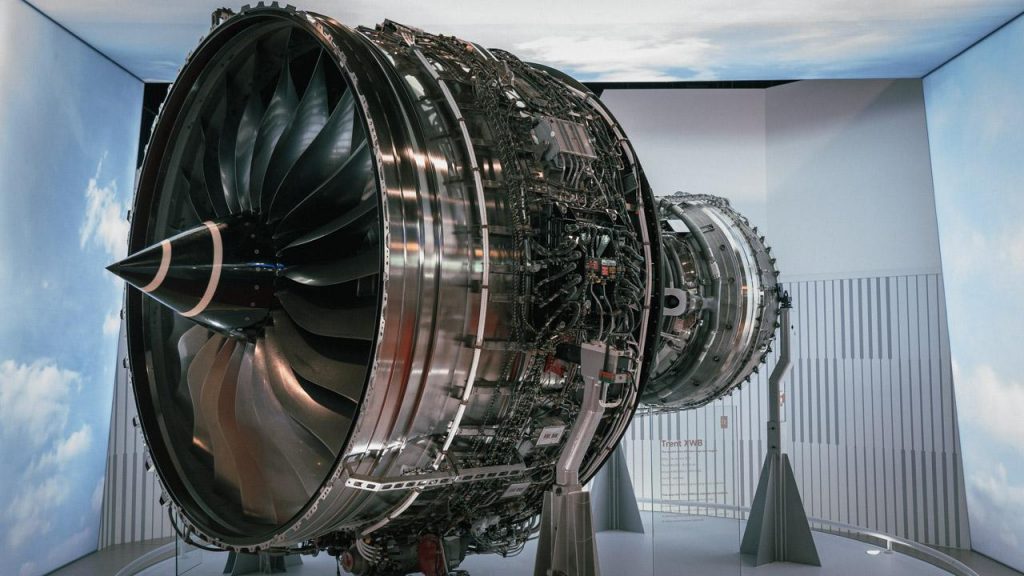
At A*STAR’s comparatively modest booth, I meet Dr. Shuyun Chng and Dr. Jeremy Yune, who work for A*STAR’s SIMTech (Singapore Institute of Manufacturing Technology). They are working on icephobic coatings—an area so bleeding-edge it has barely left the realm of academic studies.
The short story goes something like this: It’s really cold up there. Ice starts to form when the plane encounters cloud droplets. SIMTech wants to prevent this with a new material.
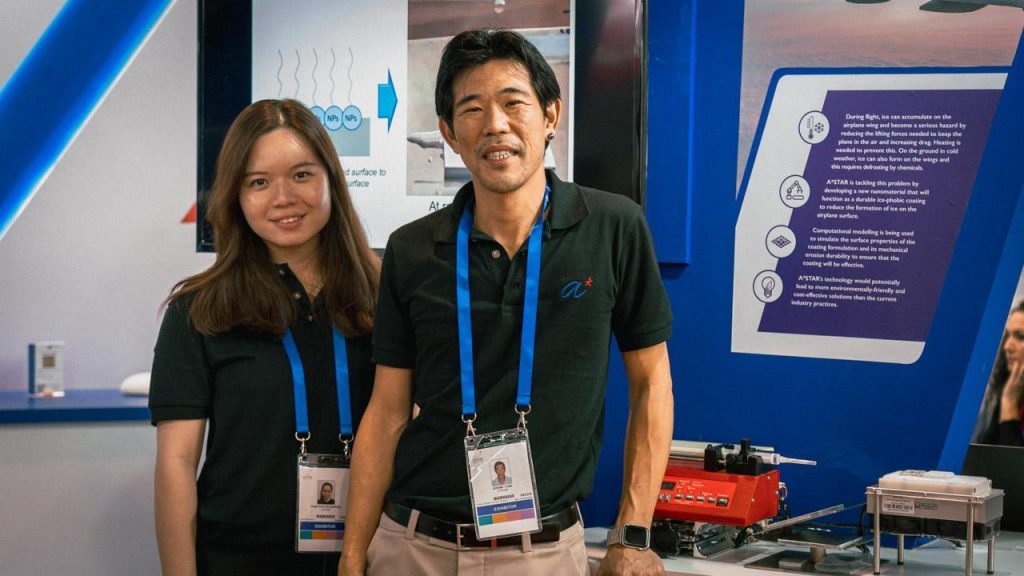
This is a pain for everyone involved.
For the pilot who has to remember to de-ice the plane before landing. For the airline who has to buy more fuel (because it takes a lot of energy to heat the wing from -50 to 0 degrees). For the airport personnel who have to spray the plane with hazardous anti-icing chemicals before and after takeoff in winter. For the passengers who will be paying for all of this—and watching their life tick away, because ice causes tens of thousands of flight delays every single year.
For those with a congenital fear of air travel, Dr Jeremy has even more bad news. Too much ice might result in the plane getting a ‘random shape’, and it has been known to cause aeroplane crashes. In fact, NASA estimates that 10% of all air crashes involve ice in some shape or another.
To solve this problem—which is as old as manned flight itself—Dr Jeremy and Dr Shuyun are developing a material which prevents what is known as ‘ice-formation’. This icephobic material is adapted from super-hydrophobic material which repels water and has been around for some years.
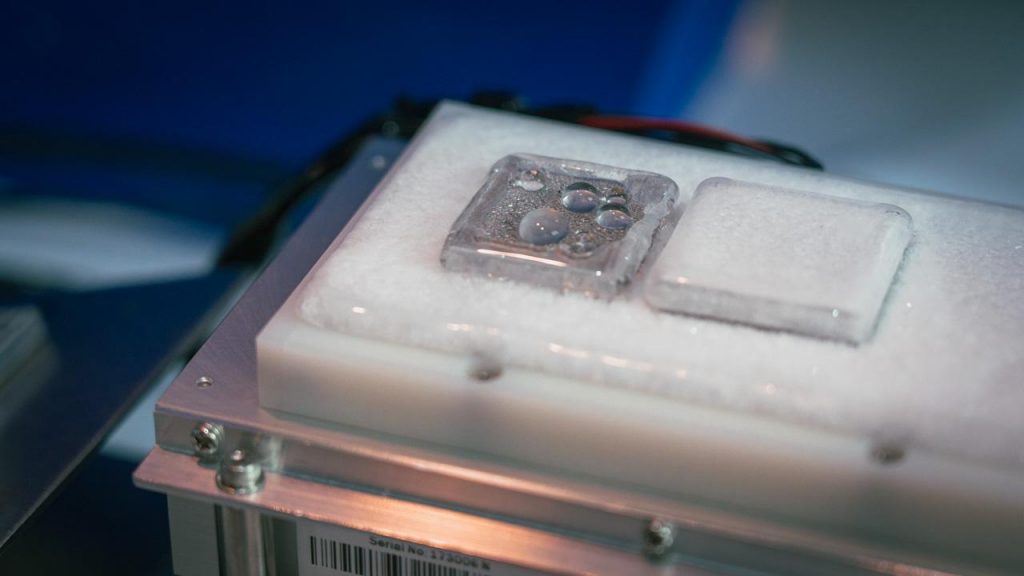
“It is great to be able to publish many wonderful papers, but what really gives us greater sense of satisfaction is to translate the technology into something that can work for the industry,” said Dr Shuyun.
It hasn’t been a smooth journey, and one of the greatest challenges comes from bridging the gap between formulations and applications, when they must—as Dr Jeremy describes—go back and forth between the science and the engineering aspects. After 3 years of work, the team enjoyed a breakthrough last year when their material proved to be resilient enough to withstand erosion and airspeeds of 50m/s.
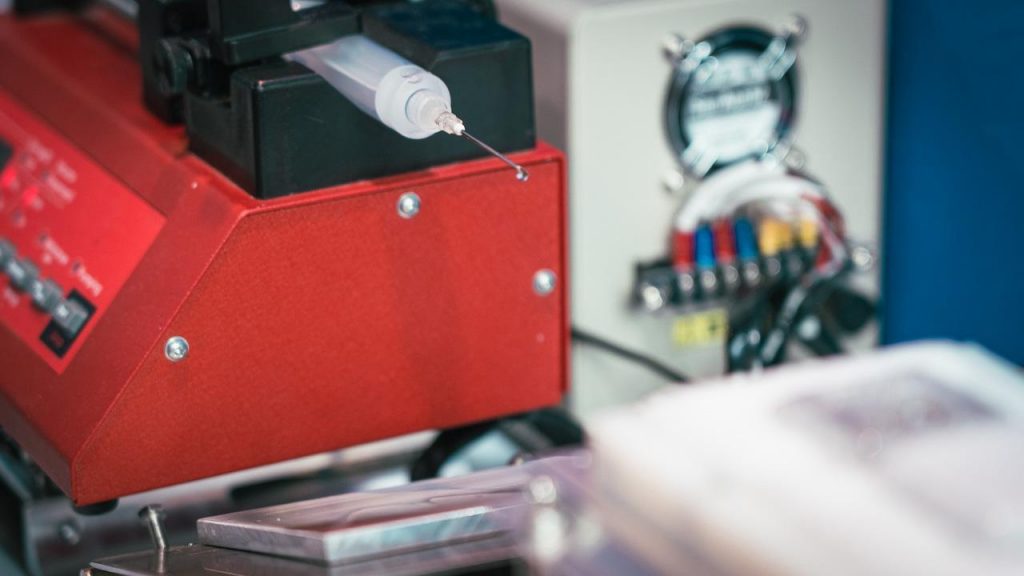
“The engineering makes us quite excited, because we see the end applications. You can proudly tell people, this is our technology,” Dr. Shuyun said.
If we keep our fingers crossed, icephobic coatings might one day revolutionise aviation technology, making travel cheaper and safer for everyone.
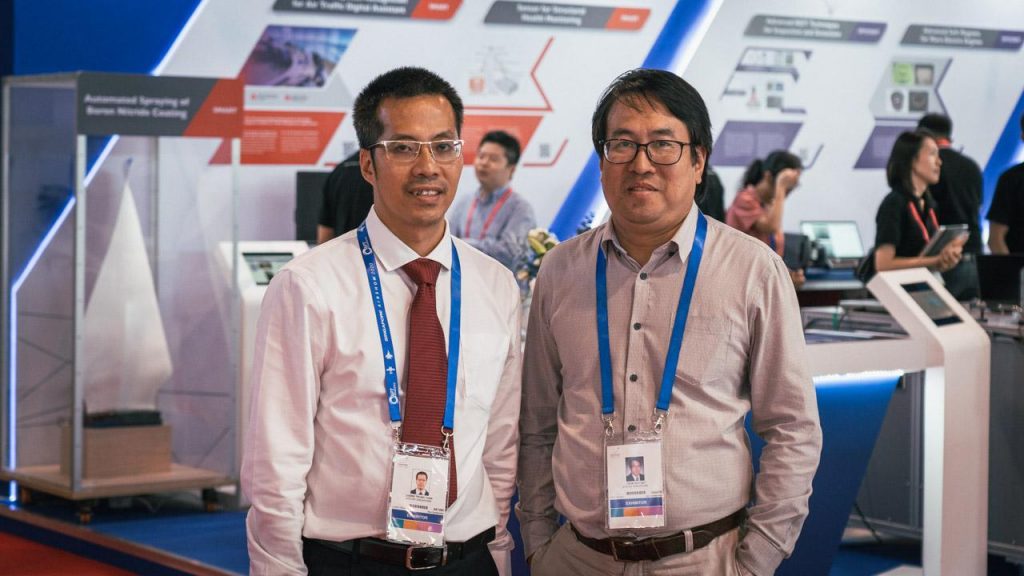
This is what I learned from the team at I2R aural & language intelligence, who are working with CAAS to integrate AI into their ATM system.
Yes. I know. I am confused too. For the uninitiated, CAAS refers to the Singapore’s Civil Aviation Authority, while ATM refers, in this case, to the Air Traffic Management. I2R is the Institute for Infocomm Research.
Once you wrap your head around the industry jargon, the heart of what they’re trying to do is actually quite intuitive. Every country has air traffic controllers and pilots. Almost every nation has its own language and accent. When a Japanese-accented pilot is directed by an Indonesian controller who speaks English as his second-language, some miscommunication is bound to occur.
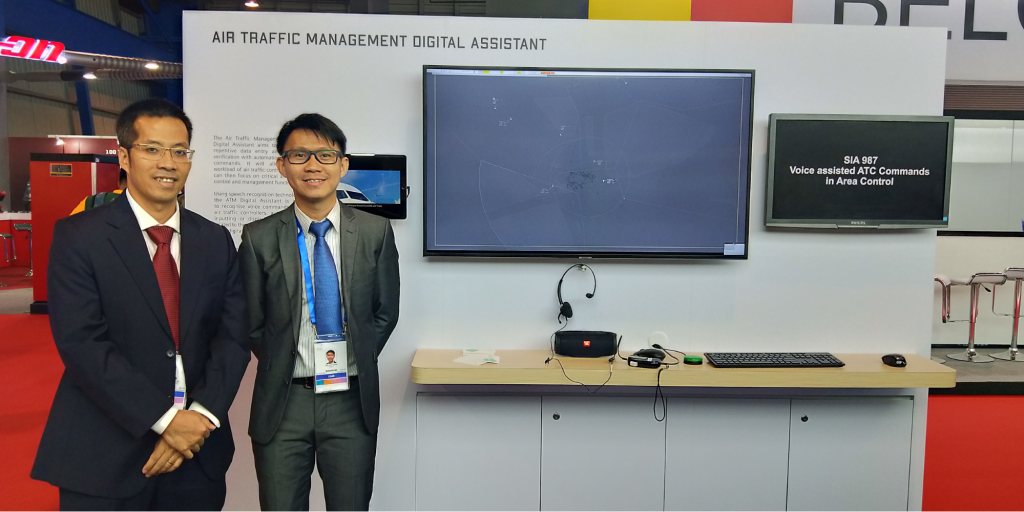
To resolve this problem, Dr Tuan and his team have developed a speech recognition system for Southeast Asian operators. It uses Artificial Intelligence to translate, say, Singlish and Malaysian-accented English directly into text, which is then updated automatically in the ATM system. How this works in practice is fairly amazing. The Speech-to-Text recognition system was made possible by advances in AI technology, but I was surprised to learn English–as it is broken–continues to present its own Challenges to ATM. You—the air traffic controller—can say in your thickest Singlish to the pilot: “descend to 40,000 feet”, and an automatic prompt will appear on screen for you to verify the information, before updating it in the system and transmitting it to the cockpit.
“Each country, each area has its own pronunciation of English, and when they try to speak English, many different variations were formed,” he explained.
Nonetheless, over the course of 3 years, the team has been able to complete a version of the Speech Recognition system that is being trialed in CAAS systems. Collaborations with aerospace manufacturers are also forthcoming, and if it proves successful, this AI will make air traffic control a safer and much more efficient process, enabling controllers to simultaneously manage more planes.
As you can imagine, such technology will have countless applications outside of air traffic control. Dr Tuan cannot foresee the future, but it’s not too difficult to imagine the possibilities.
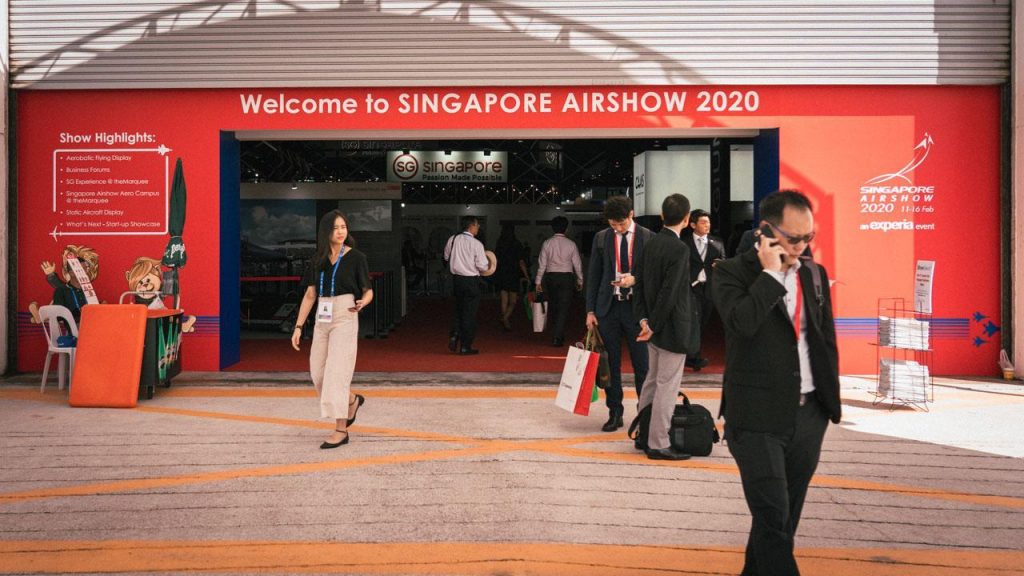
While business might have slowed down, the research being done by A*STAR has not. In another 3 to 5 years, some of the technologies available might be used to power your vacation in Bali or that business trip to Hanoi. You might never actually see it in action during your journey, but the aerospace industry is constantly changing and innovating. Many of the trends we often hear about, like AI or environmentally-friendly materials, are being adapted for aerospace as well.
The potential is limitless. After all, the conditions for aerospace are much more challenging because you’re airbourne at 60,000 feet. If you could produce a super-hydrophobic material for commercial airlines or a speech-recognition system that works with VHF, imagine the wider possibilities back on earth.
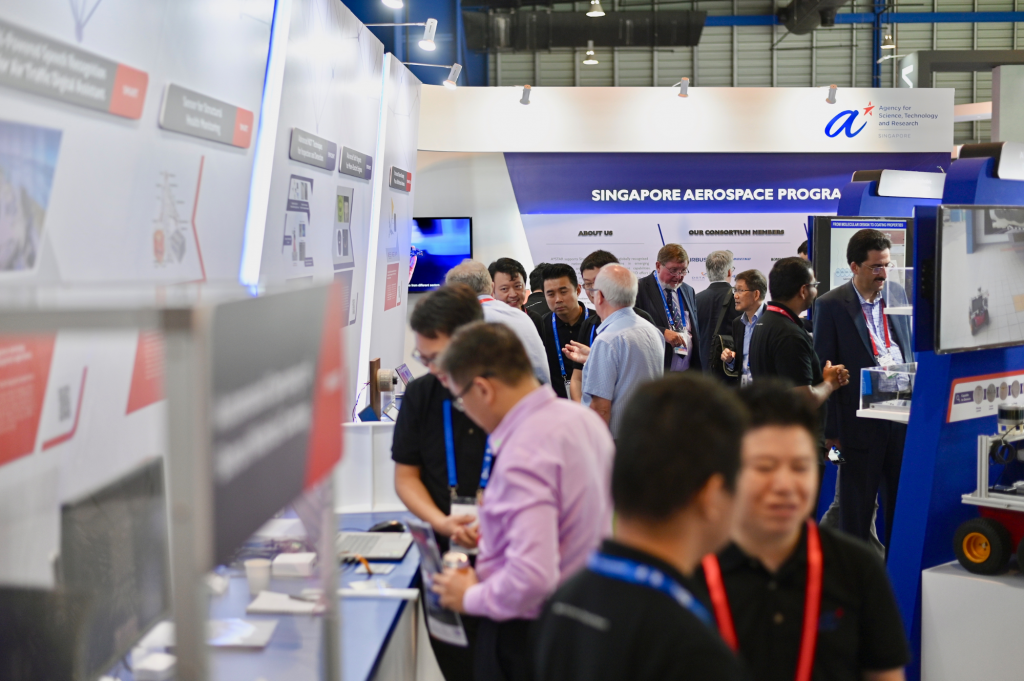